In December 2015, the Westgate Tunnel Project (WGTP) was announced, with construction planned to commence in 2018.
The project became the flagship for the ‘Big build’, a rail and road infrastructure program created by the Dan Andrews Government, which includes such projects as Melbourne Metro Tunnel, Suburban Rail Loop and North-East Link.
The WGT Project would require almost unprecedented quantities of construction materials, in a relatively short time frame. The Boral team in Melbourne identified the unique opportunity to be involved in this city shaping project, and began negotiations with the Primary Contractor, the CPB John Holland Joint Venture. Our challenge, to supply and install 600,000 tonnes of Asphalt, 400,000 cubic metres of concrete, and 800,000 tonnes of rock and recycled roadbase products
The project scope is a unique combination of 3 main elements
- Reconstruction of the Westgate Freeway from the M80 Ring road to the Westgate Bridge.
- Two 4km underground tunnels, with associated portal and vent structures
- A bridge across the Maribyrnong River and elevated roadway along Footscray Rd into the CPB
Five years later, Boral has become a key part of the projects success, despite the well publicised and long running issue with contaminated soil which has significantly delayed the project.
The team at Boral asphalt constructed and have operated a high capacity mobile asphalt plant located at Deer Park to replace the entire length of the Westgate Freeway from Altona North to Yarraville. For context, this is 8kms of 12 lane freeway. No mean feat considering that traffic flow had to be maintained at all times. What’s more astonishing is that underneath the asphalt layers is 500,000 tonnes of recycled brick and concrete (enough to fill the MCG to the very top), courtesy of Boral recycling.
On the other side of town, Boral’s concrete operation at West Melbourne, has been busy batching and delivering a raft of high durability low carbon concrete mixes to the tunnel portal structures and the elevated roadway section of the project. To date, Boral has achieved an average 40% reduction in cement through the use of GGBFS and Flyash, a really significant contributor to the projects sustainability targets.
In some areas, concrete is required to meet strict durability specifications whilst also being easy to place, presenting a number of challenges to the Boral product development team. Within the tunnel itself, roadway support corbels are being installed using Boral’s high durability steel fibre reinforced concrete, a unique solution requiring a tight quality management regime.
The project is expected to be completed in 2025, and Boral still has a big part to play in the final stages. The project has been a great success for Boral to date, but the real value has been in the way multiple teams within the business have collaborated to meet the project demands and high standards. A big congratulations to all involved so far.
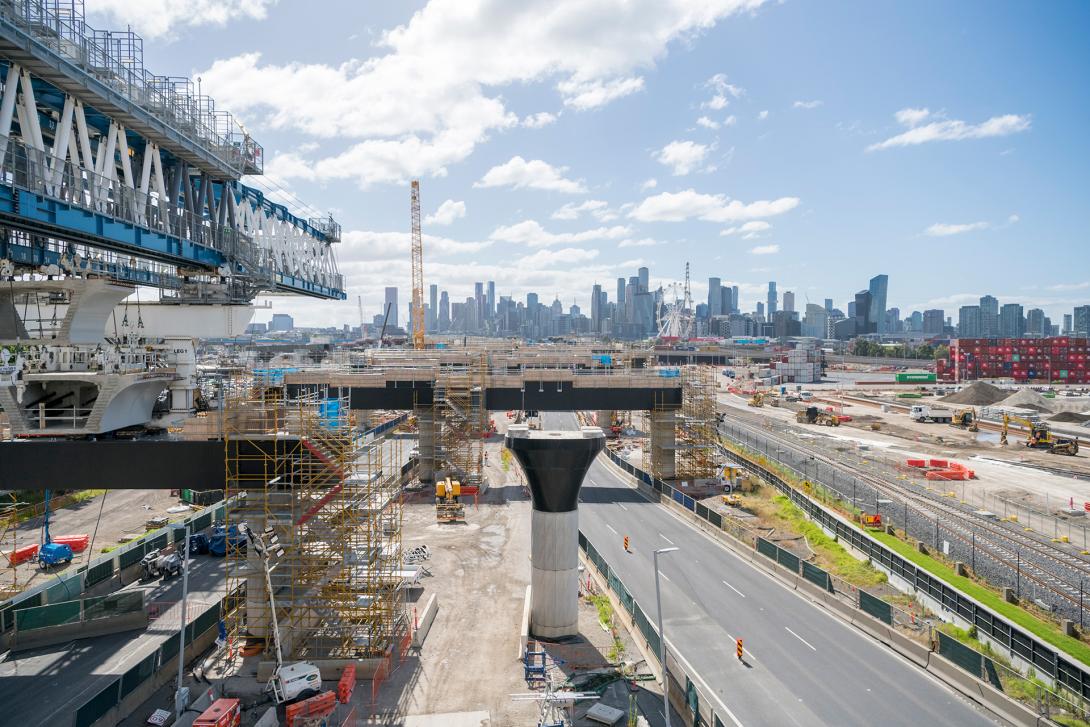