“This is the beating heart of concrete testing,” proudly exclaims Ben Gow, Head of Technical Services, as he walks into the concrete testing area of the Baulkham Hills Boral Materials Technical Services (BMTS) Laboratory.
Around us, are various tanks of saturated lime solution, containing hundreds of fourkilo samples collected from across worksites mainly in the greater Sydney area, but also including samples from across Australia. The facility processes about 10,000 samples a month (with all used and processed samples ultimately being recycled through our Widemere facility).
In the nearby drying shrinkage room, concrete samples sit in a temperature and humidity-controlled room which simulates the effects of shrinkage. Other samples are subject to static load, to be assessed for creep.
“Concrete is brittle, so the less shrinkage the better from a design perspective … Envisia for example has 40 per cent less shrinkage,” he says.
“This is a key room and provides us with data. It helps us and our customers test for product hardened properties. Customers involved
in infrastructure, and medium and high-rise construction are testing constantly – we have 40 of our people out in the field every day bringing in samples every day.”
Indeed, inside the Baulkham Hills lab there is a veritable hum, with the 50 or so onsite employees hard at work across the facility’s chemistry, cement, aggregate, concrete, soil and asphalt laboratories.
The BMTS facility, which operates six days a week, specialises in compliance testing of construction materials and offers quality control testing, along with R&D expertise.
Ben estimates about a third of Boral’s profit can be attributed to the work done in the lab – the oldest accredited construction materials lab in Australia, and arguably the largest of its kind in the Southern Hemisphere.
“This lab offers a significant proportion of its services external to Boral, about 25 per cent of our business comes from external customers,” he says. “We are known in the industry as the premier commercial lab.
“Here we can reverse engineer concrete, where we can be given a sample and then through concrete analysis, break it down and then be able to come up with the mix design, validate it and then test the concrete to show it will meet spec.”
The lab provides a full gamut of services, ranging from chemical analysis of water to comprehensive environmental services such as gravimetrical and directional dust monitoring.
In addition to the concrete lab, the facility has an aggregate lab that handles verification testing, along with friction coefficient and resistance testing – which is critical for airport roads and runways.
“All this testing comes together to provide an indication of the performance and durability of the material,” Ben says.
In the soil and materials testing lab, the team characterise materials to determine strength and stability, important considerations when it comes to compaction.
While in the asphalt lab, compliance and characterisation testing runs almost continuously for various airport projects Boral is delivering solutions for. Various testing machines measure wheel tracking and rut depth, fatigue life and elasticity at higher temperatures.
“The testing for airport projects is important given our work with Western Sydney International Airport and other key airport projects nationally.”
In fact the lab and our people have been sought out from across the globe.
The BMTS facility was used to conduct specialised creep testing of the high strength concrete used in Dubai’s Burj Khalifa – the tallest reinforced concrete building in the world.
“It’s a great team here and a fantastic lab – it’s a real asset to Boral.”
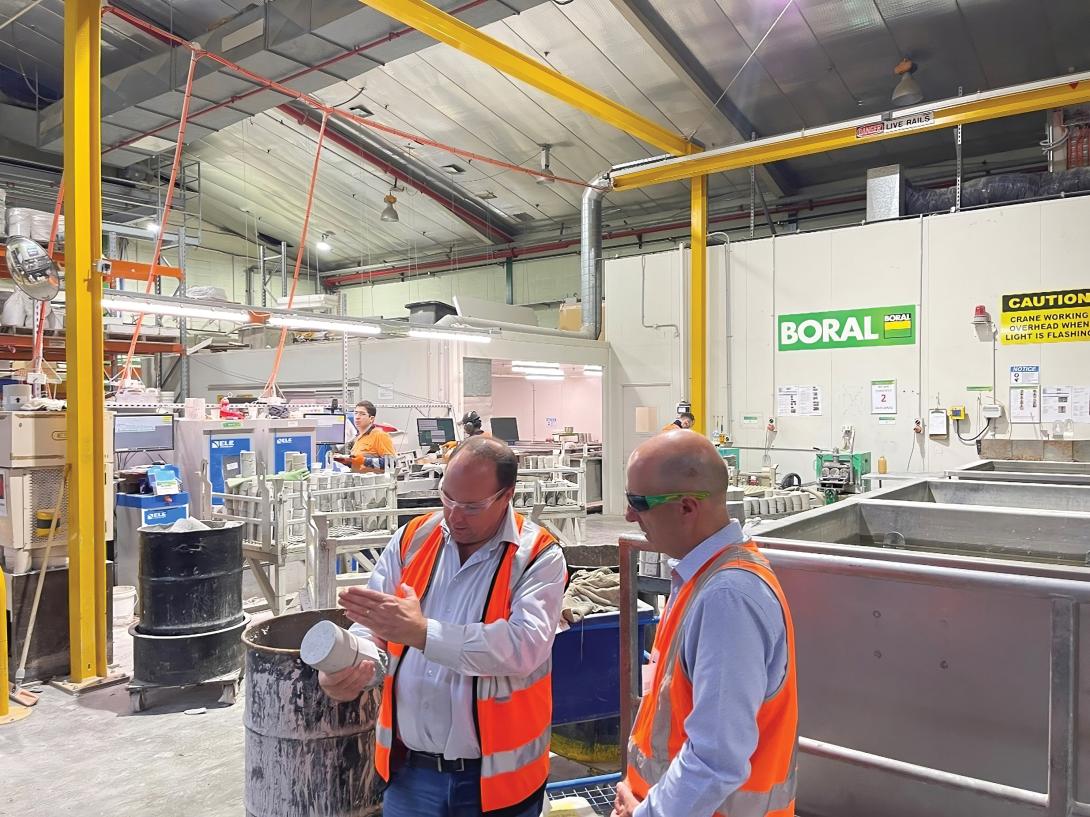
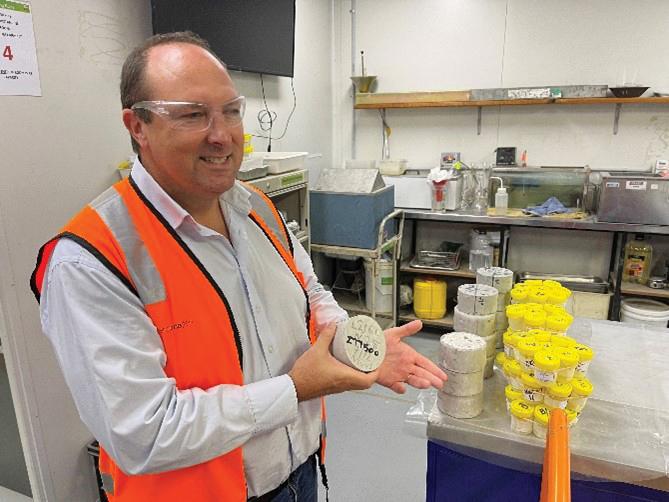