Boral is revolutionising the way we deliver concrete across Australia, resulting in improved service to our customers and increased transport efficiency.
An enterprise standardisation program, Automated Allocations, is introducing world-class transport technology and reimagining the way our concrete allocations teams work. It is all about making it easier for our people to schedule and dispatch concrete deliveries efficiently.
Getting the right truck to the right location with the right product in a dynamic construction environment is no easy feat.
One of Automated Allocations first steps to success has been to focus on the digitising and connecting a myriad of trucks, products, plants and customer information to create a sole source of correct data.
This information is then fed into our new Automated Allocations solution, which uses an algorithm, like a giant calculator, to recommend the best transport schedule, considering customer service and transport efficiency.
And a bit like when you go off course when using Google Maps, Automated Allocations solution then re-optimises the schedule in real time when a change occurs, like when a pour runs over time or if there are traffic hazards.
A key benefit of the new Automated Allocations solution is the pre-planning capability as it provides Contact Centre, Operations and Sales teams with a shared view of the advanced schedule. The visualisation tool allows collective decision making, in support of achieving the best balance between customer experience and transport efficiency.
The Automated Allocation program has recently been implemented in our metropolitan Concrete plants in Queensland, Western Australia, Victoria and South Australia, with metropolitan New South Wales scheduled for June.
Early data is showing good improvement in customer service through delivery on time and increased transport efficiency. Further improvement is expected as we imbed the program, and we go from good to great results.
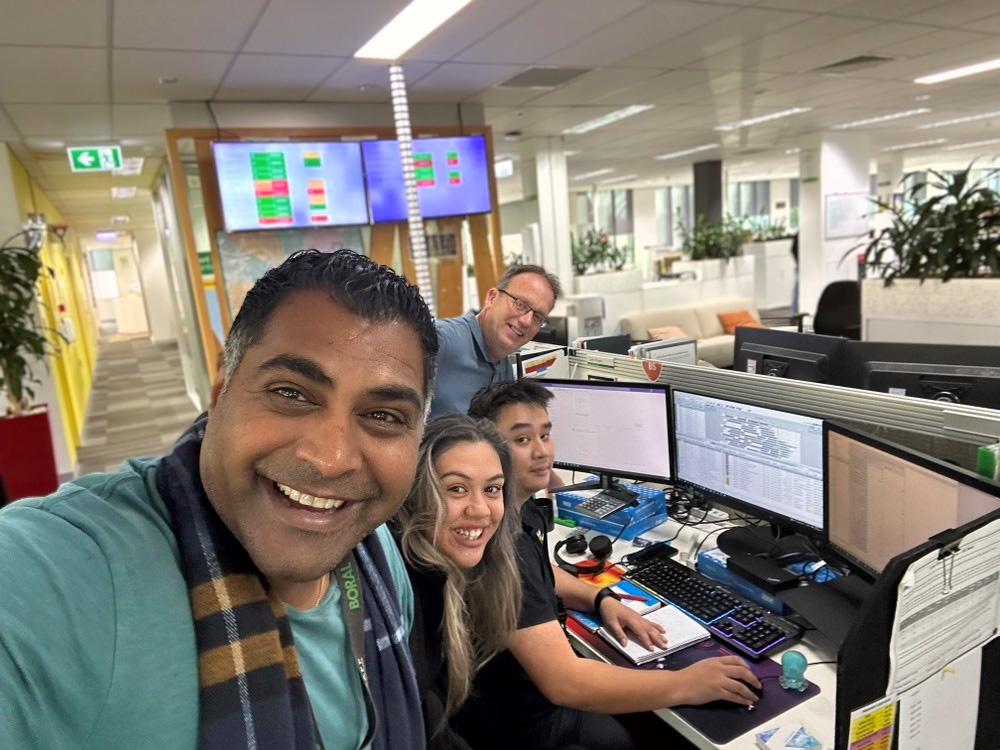
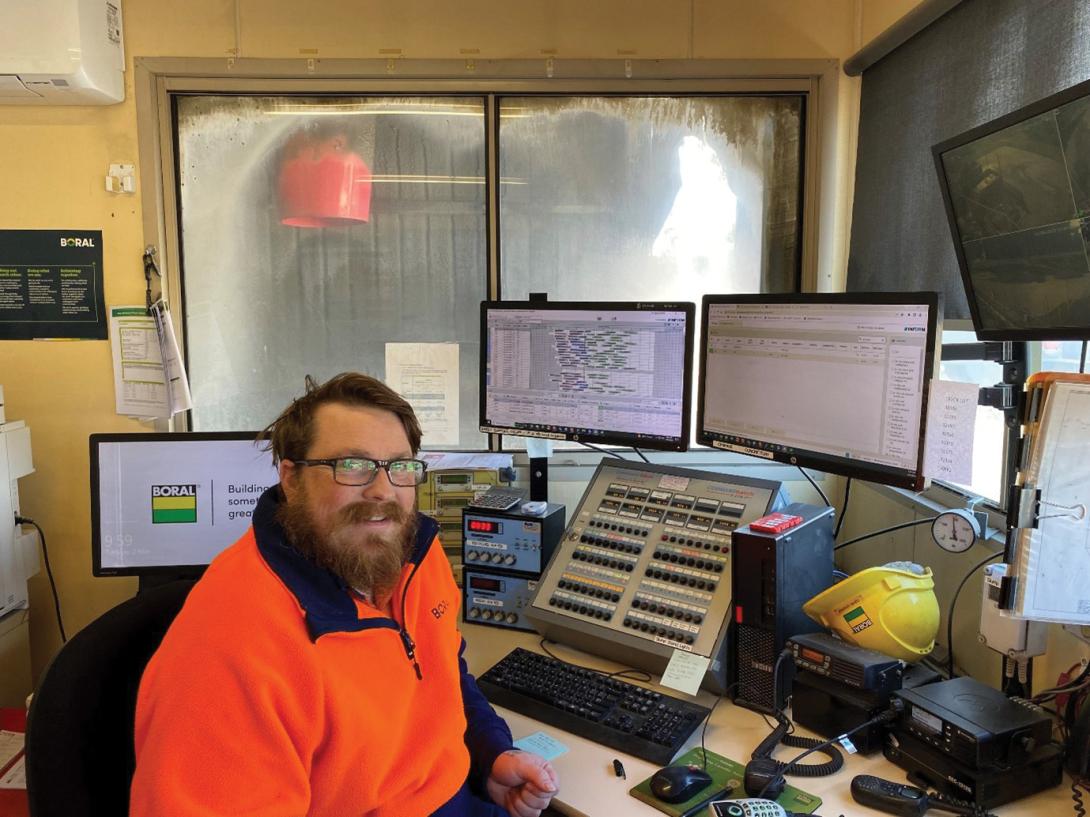