Go behind the scenes on this million-dollar-a-day project
The Berrima Cement Works, located in the Southern Highlands region of NSW, produces more than 60 per cent of cement products in NSW and the ACT.
Operating with one kiln, the Works takes limestone delivered by rail from the Boral Marulan South Limestone Mine, and after blending it with other materials, burns it at high temperature to produce clinker. Clinker, in the form of pellets, is ground to produce the cement powder and construction products you may be more familiar with.
Each year, the site undergoes an intensive annual shut down for maintenance on the kiln, a critical operation that ensures the plant runs efficiently, safely, and reliably for the year ahead.
This complex event involves months of planning, precise execution, and the combined efforts of hundreds of people from diverse teams at Berrima and across the business.
Key components of the Shutdown
If you ask Engineering Manager Renier Cronje, planning for the annual shutdown starts the day after the previous one ends!
The planning involves developing a list of tasks to be completed in the shutdown based on previous shutdowns, our routine maintenance schedules, or any emerging issues identified through inspections throughout the year.
The project includes major equipment overhauls, refractory work in our cement kiln, mechanical and electrical upgrades, and capital project installations. This year, for example, we had planned to replace 48 metres of kiln brick lining, with inspections of the kiln lining status, meaning that might extend to a further 10 metres. Major capital work took place to replace the alternative fuel feeding system bin by using 500-tonne crane.
Managing risks and making sure everyone gets home safely
With up to 500 contractors on-site alongside our core teams, safety is at the forefront.
The team need to manage high-risk activities including traffic management and exclusion zones, stored energy, confined space entry, and working at heights to name just a few. Strict barricading, atmospheric monitoring, spotters, and detailed lock out and tag out procedures are all in place and safety protocols are rigorously followed to ensure everyone goes home safely.
The Shutdown by numbers
Duration: 23 days (including cooling down and commissioning), with daily meetings to review prior day and set plans for day ahead.
Contractors on-site: Around 300 but up to 500 at peak times
Cost: Approximately $1 million per day
Major Tasks: Kiln brick lining, Preheater cyclones, mechanical and electrical upgrades
Shifts: 12-hour rotations to maintain 24/7 progress
Teams involved:
- Mechanical, Electrical and Refractory engineering teams
- Production teams
- Shutdown planning, capital and Asset teams
- Tradespeople and teams
- Safety team
- Procurement team
- Contractor Management and site supervisors
Operation Manager Waqas Ali said “The success of Berrima’s shutdown comes down to great planning, teamwork and a shared commitment to safety.”
“Anyone who has worked a shutdown would say - it’s a really challenging but very rewarding process and one that ensures our Berrima plant runs smoothly for the year ahead.”
Go behind the scenes
See what it was like at Berrima during this mammoth effort in our documentary below.

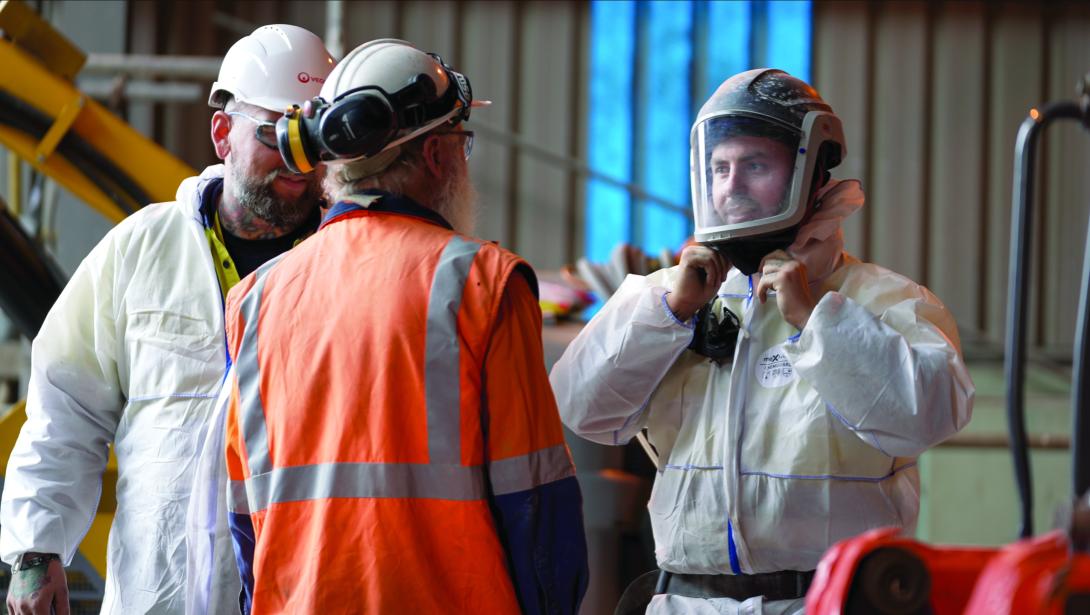
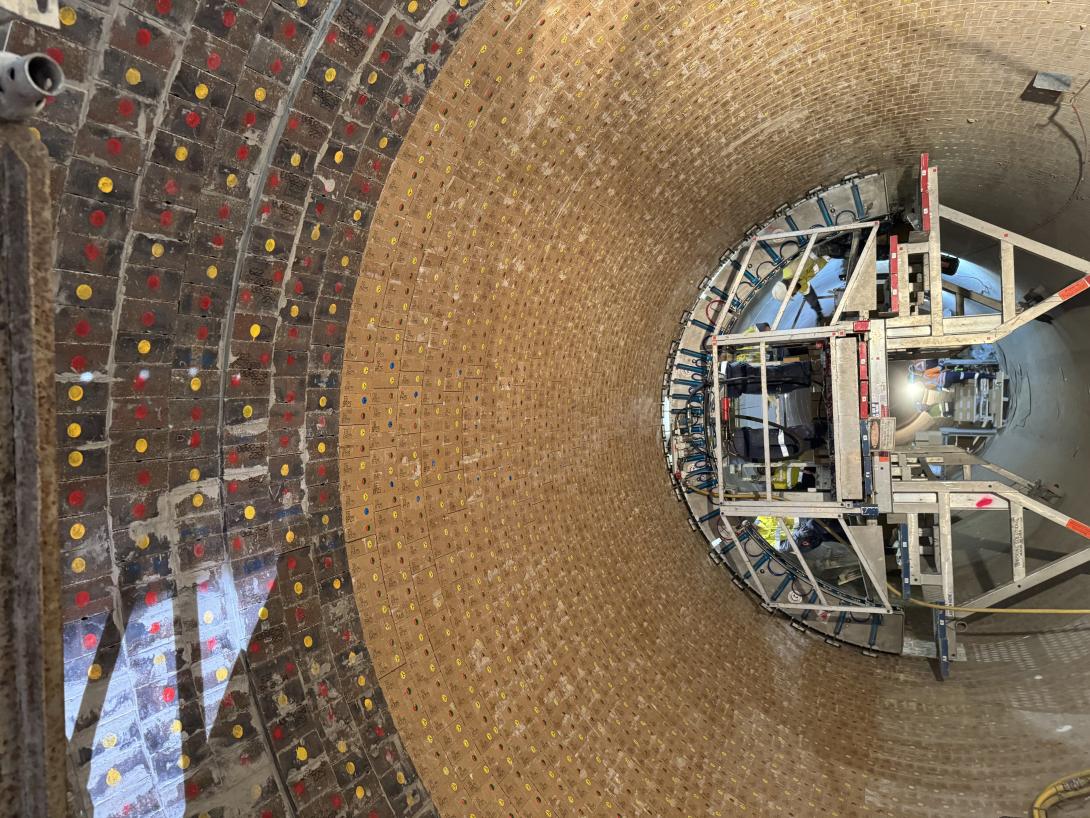
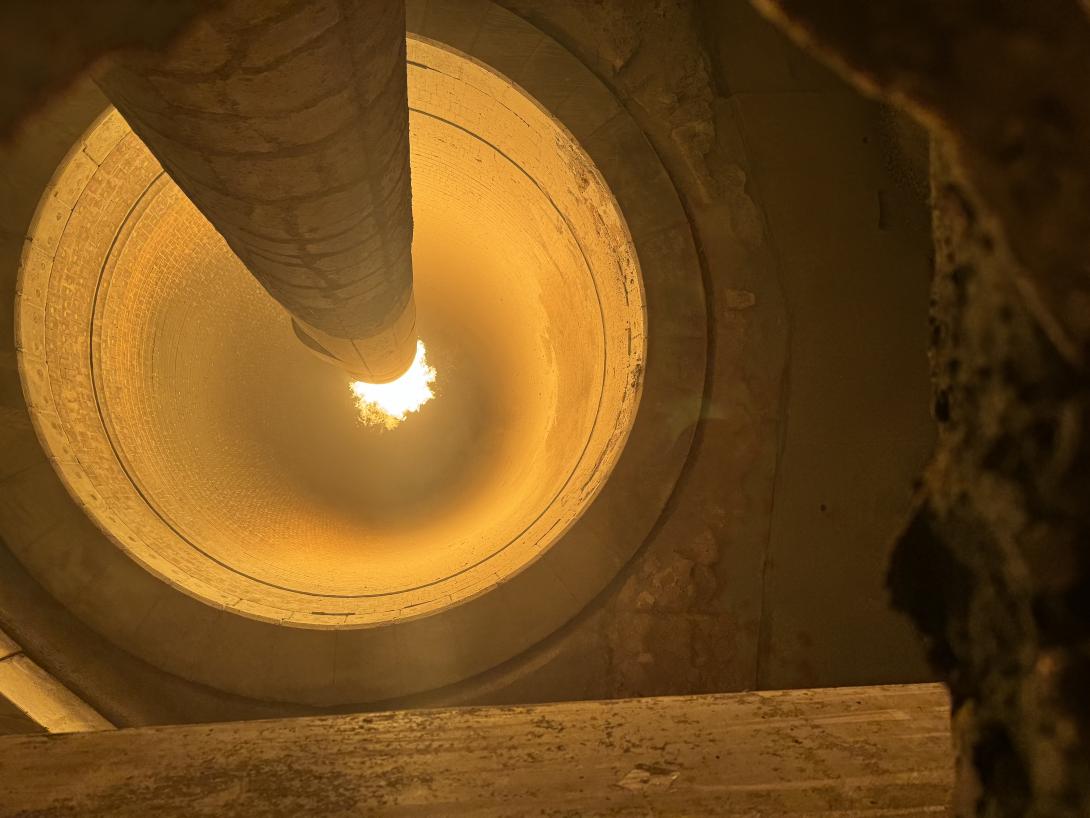
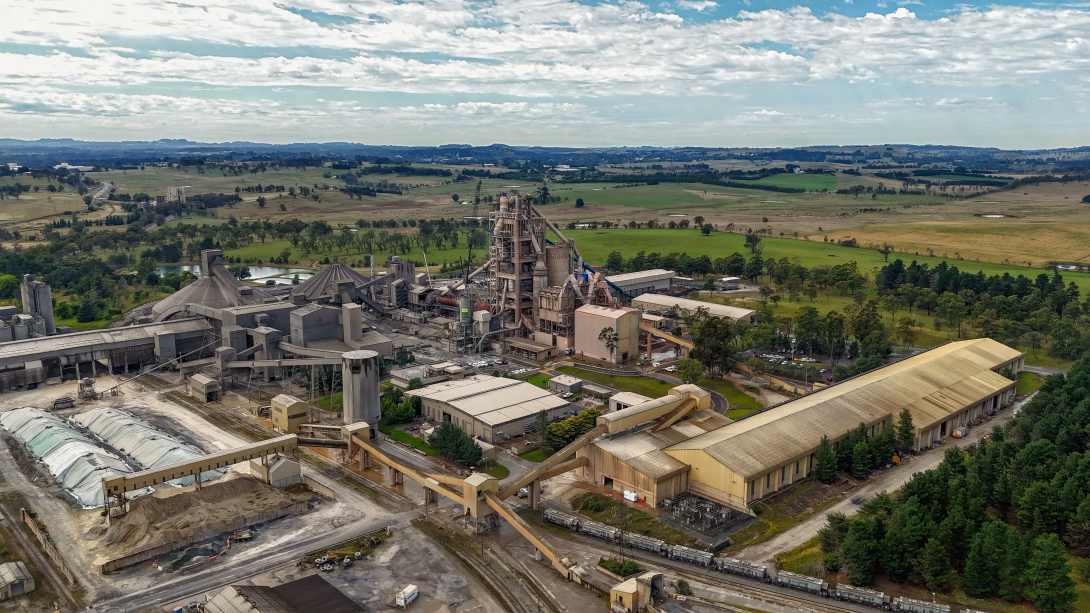
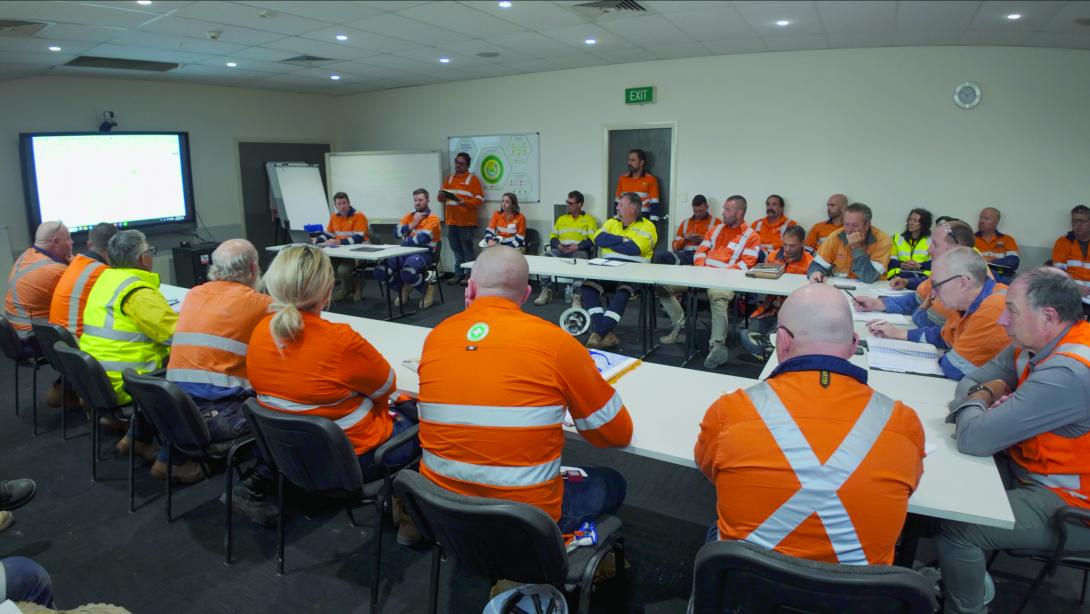
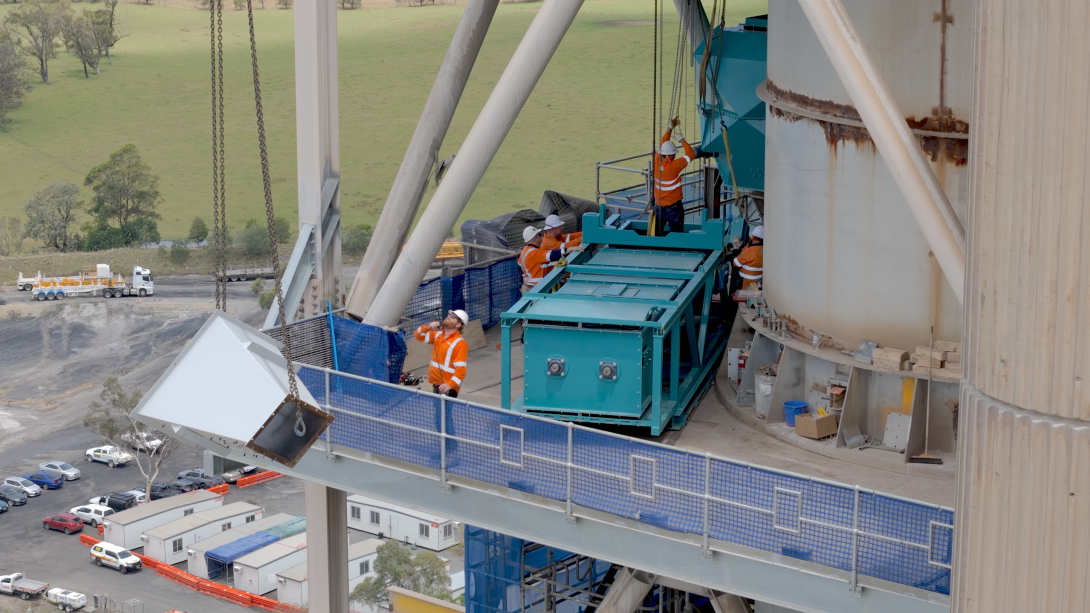