In the last 18 months we’ve invested significantly in new laboratory technology across Asphalt. The new equipment allows the team to increase testing capability and better manage industry and customer technical developments, and the demand for more sustainable product offerings.
Our teams in Baulkham Hills (NSW), Deer Park (VIC) and Narangba (QLD) have been busy commissioning the new testing equipment, establishing proficiency and gaining the required certification from the National Australian Testing Association(NATA).
State Technical Managers and Laboratory Supervisors have been busy setting up the additional technology, which is also alleviating demand on our production site laboratories helping these teams focus on the compliance of our daily product supply.
The arrival of new “superpave” compactors in each state, including SA and WA, will lead to a significant reduction (and potentially elimination in the future) of the repetitive, cumbersome and manual compaction test procedures currently performed in our production laboratories.
Because of the new technology, our team in Victoria has also been able to significantly increase the RAP (Reclaimed Asphalt Pavement) that they are able to recycle into our asphalt mixes. It’s a requirement of high percentage RAP mixes that the final viscosity of the combined bitumen blend is accurately controlled. Our newly acquired DSR (Dynamic Shear Rheometer) device at Deer Park allows the team to make this check and ensure the product meets Department of Transport and Planning Victoria requirements, in a time effective manner.
In Queensland, the Department of Transport and Main Roads has adopted a High Modulus Asphalt (EME2) technology almost exclusively in all base course asphalt across Metropolitan Brisbane. EME2 has an important performance-based design element, optimising flexural stiffness and fatigue. Being able to conduct testing at Narangba is helping us deliver more effective and timely design changes.
Our Baulkham Hills laboratory has commissioned a new Hamburg Wheel Tracking device which provides a more robust assessment of our mixes and tests their ability to withstand deformation and moisture. The device specimens to 50-degree temperatures, all while fully submerged in water. This test is a key test parameter in the recently approved Austroads test protocol to assess the replacement of hydrated lime with non-traditional adhesion agents/additives. Being able to replace hydrated lime will improve both technical and commercial outcomes for Boral and importantly is also a key step on our decarbonisation journey, with the opportunity for a large reduction in carbon footprint with these mixes.
The new binder pressure ageing vessel at Baulkham Hills measures the durability of our binders and is important in the development and performance of crumb rubber modified binders to help us deliver higher performing mixes.
National Sales Manager Asphalt Rob McGuire said of the investments “While these investments in our lab equipment are driving better outcomes for Boral, our customers and the planet, the active involvement and engagement from our laboratory teams has been the greatest part of this initiative as we continue to build something great in the asphalt business.”
Thanks to our leaders and teams for ensuring this new technology is managed on site
State Technical Managers - Dan Smith (Queensland), Duncan Findlay (NSW), Marc Boswell (Victoria)
Laboratory Supervisors - Austin Watt (Queensland), George Prudnyk (NSW), Hassan Akhlaghi (Victoria), James Korner(SA) and Zahir Bouali (WA)
And to all our Asphalt lab teams – thank you
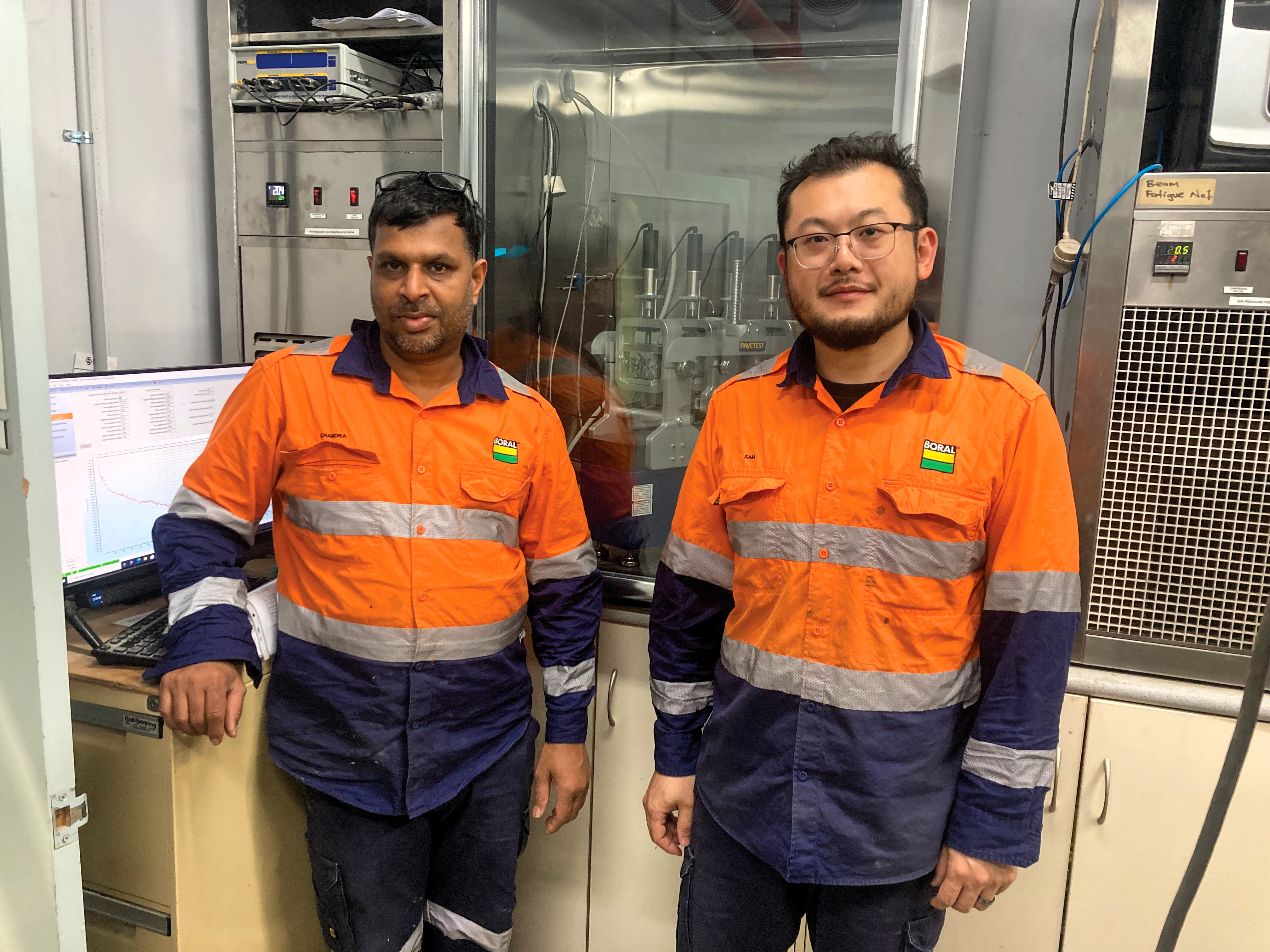
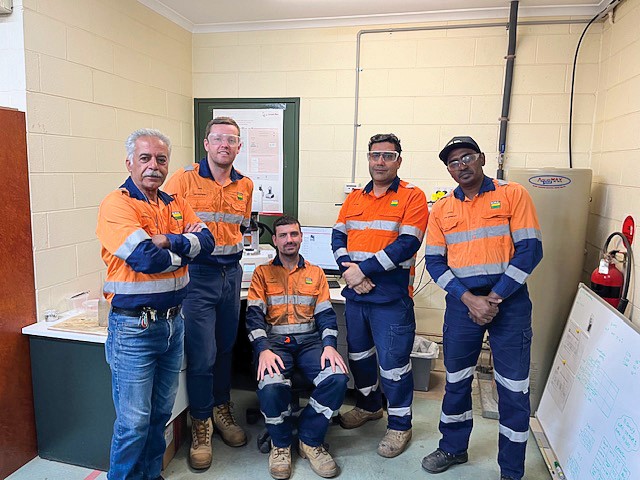
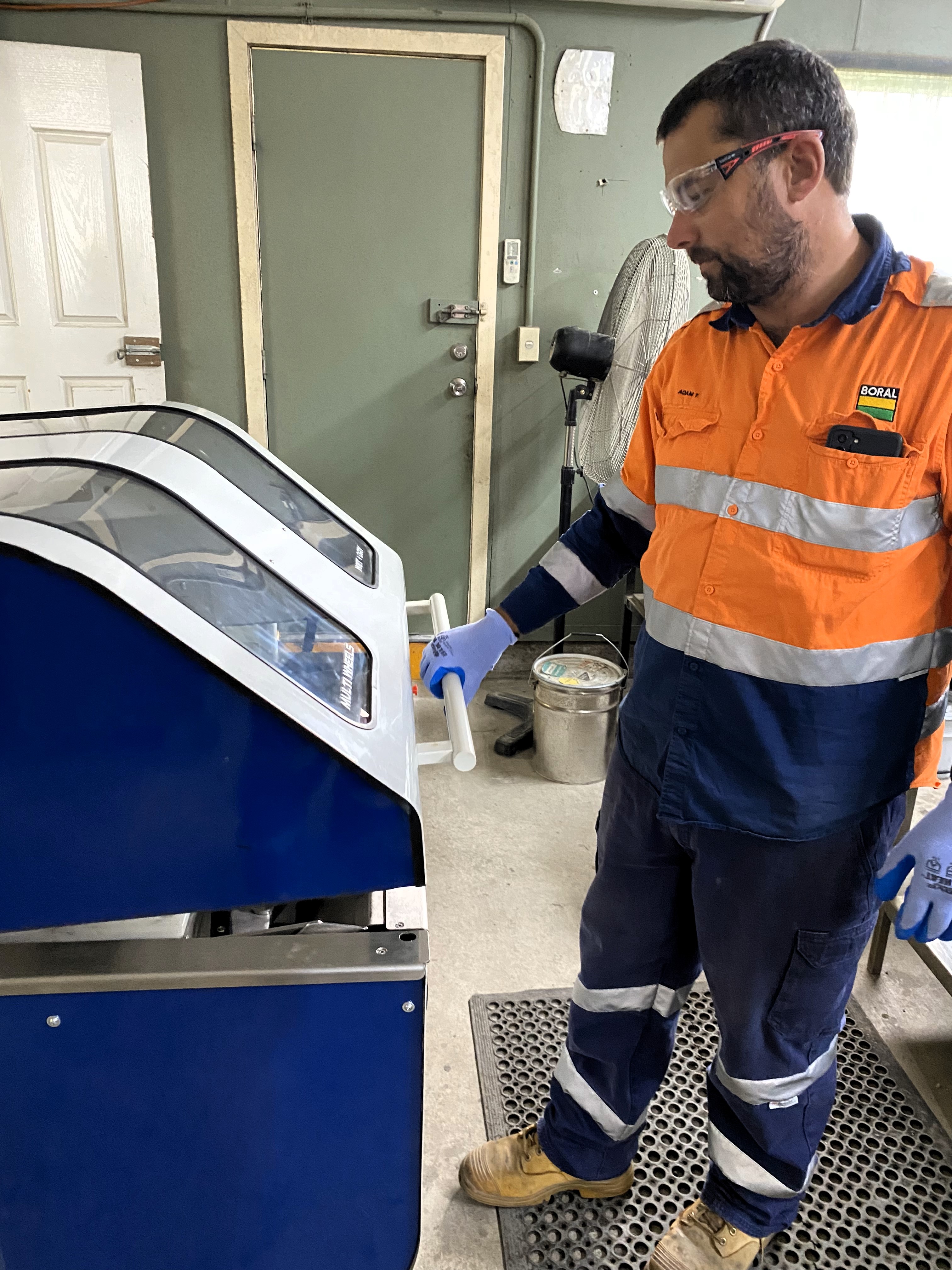